Before adding SKU Inventory Information and adjusting Inventory, warehouse and location information need to be set up in advance.
How to Set Warehouse?
① Go to the setting icon> Go to "Inventory Settings"> Click on "Create"
② Fill the comments, warehouse and address details in the red frame> Click "Save"
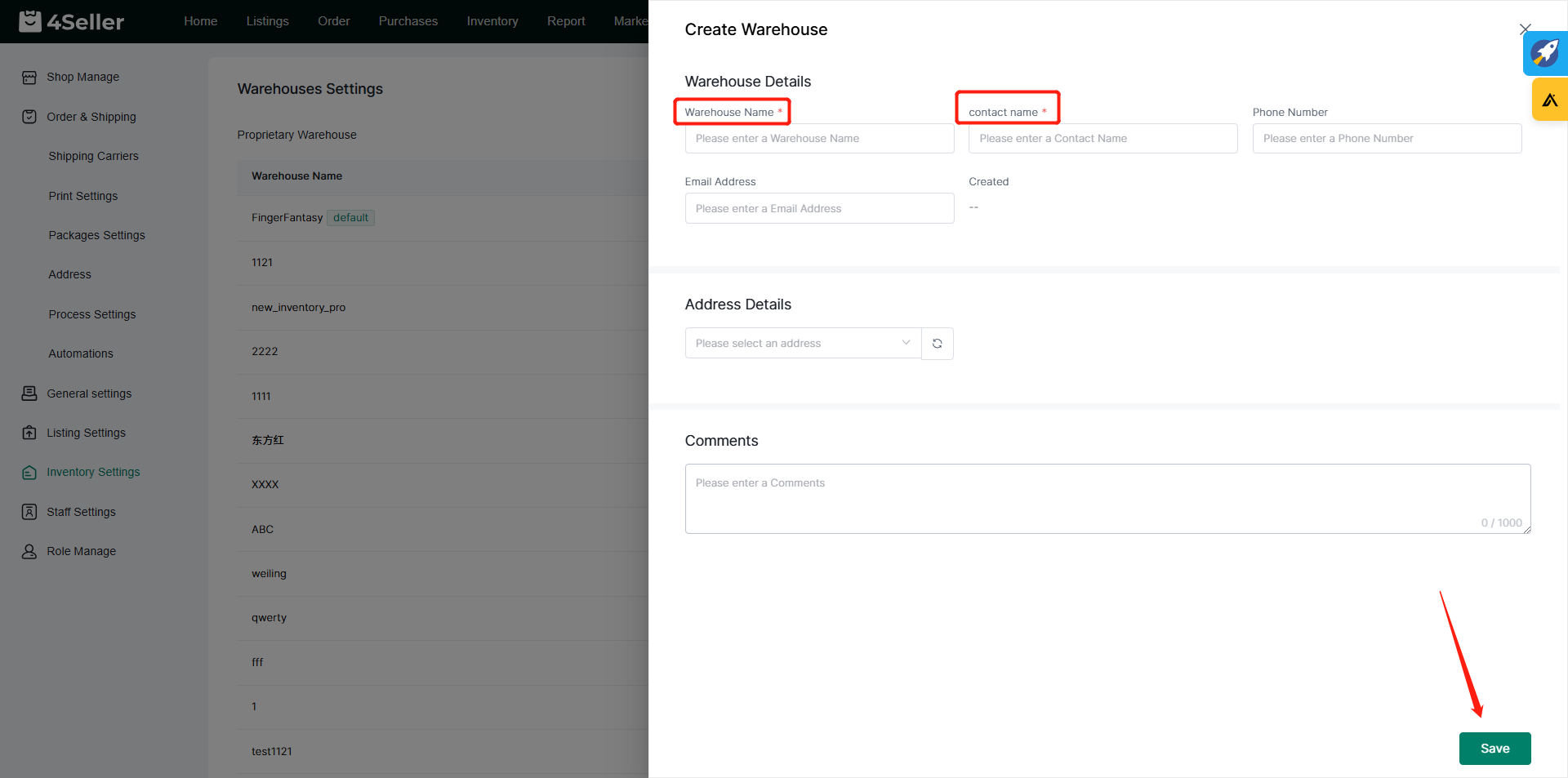
How to Set Location?
① Go to the setting icon> Go to "Inventory Settings"> Click on "Stock Location"
② Fill the address, capacity and comments information> Click on "Save"
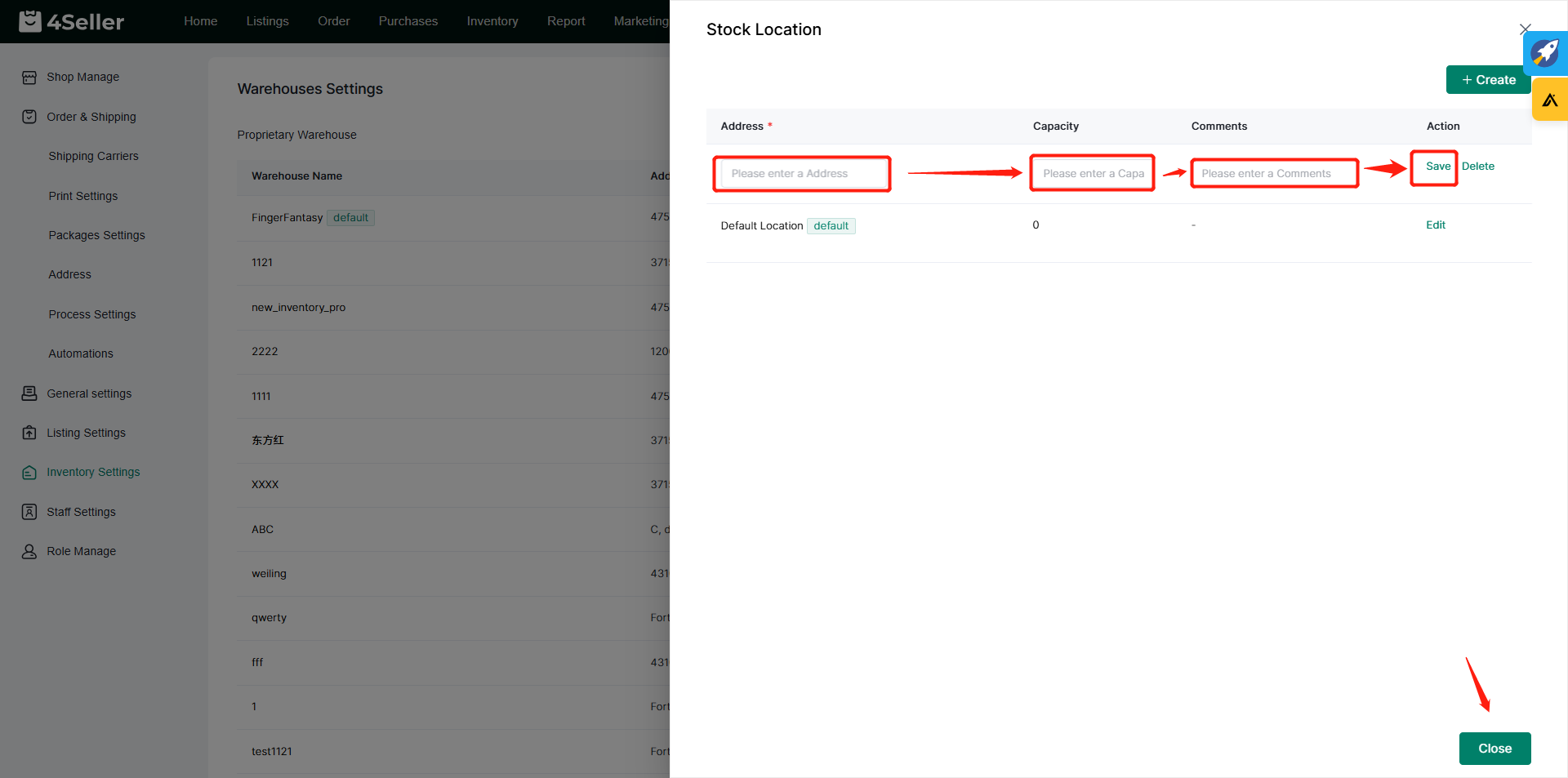
How to Add SKU Inventory Information Individually?
① Go to "inventory"> Click on "Add Inventory"
② Select the warehouse> Click on "Add SKU"
③ Search by product name or SKU to select SKU> Select the product you want to add> Click on "Confirm"
④ Select the location from the dropdown menu> Fill the "On Hand Quantity" and "Unit Cost" in the red frame> Click on "Done"
- If multiple SKUs are selected, click "Bulk Edit" to batch edit all SKUs information including "Location, On Hand Quantity and Unit Cost" in the list.
How to Add SKU Inventory Information via Template?
① Go to inventory> Click on "Import initialize"
② Download the inventory template
③ Fill the SKU, warehouse Name, Location, On Hand Quantity and Unit Cost into the Excel spreadsheet
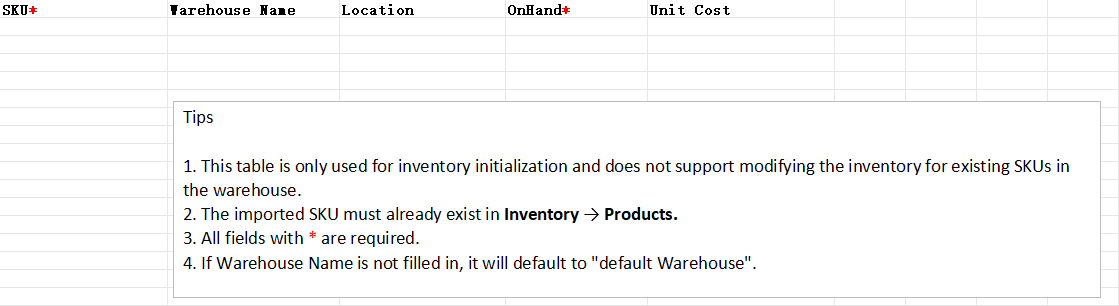
④ Upload the Excel spreadsheet> Click on "Import"
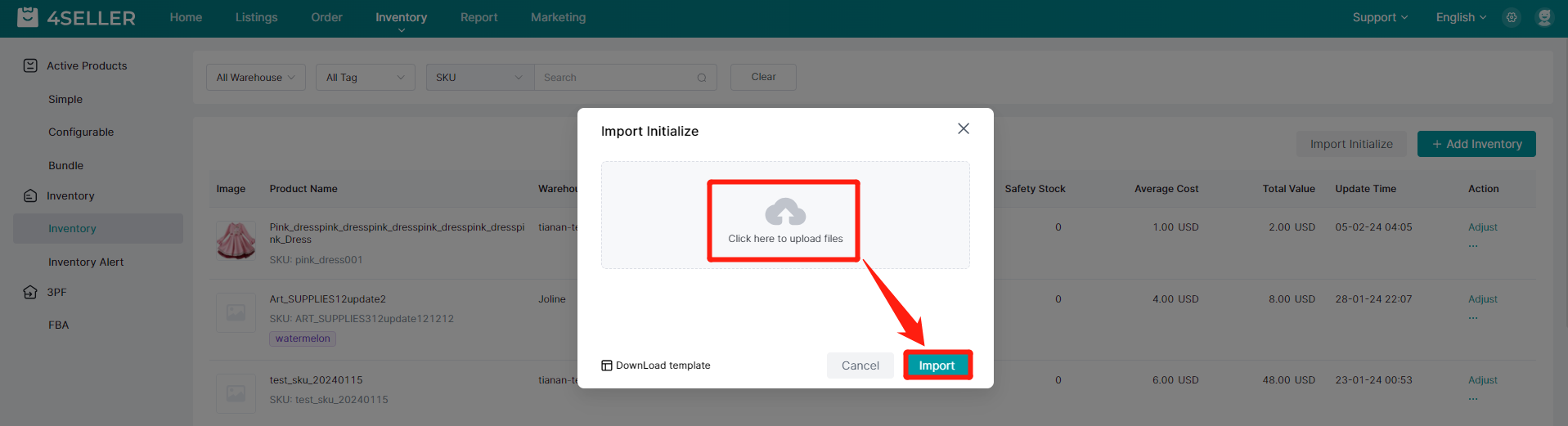
How to Adjust Inventory Individually?
① Click on "Adjust"
Click "Adjust" to adjust the inventory information including the "Location, On Hand Quantity and Average Cost"
Click "Delete" to delete the whole product inventory information
② Change the location onhand quantity and average cost information as you want> Click on "Save"
③ The modified "Warehouse Name, On Hand Quantity and Average Cost" will be displayed in the warehouse list.
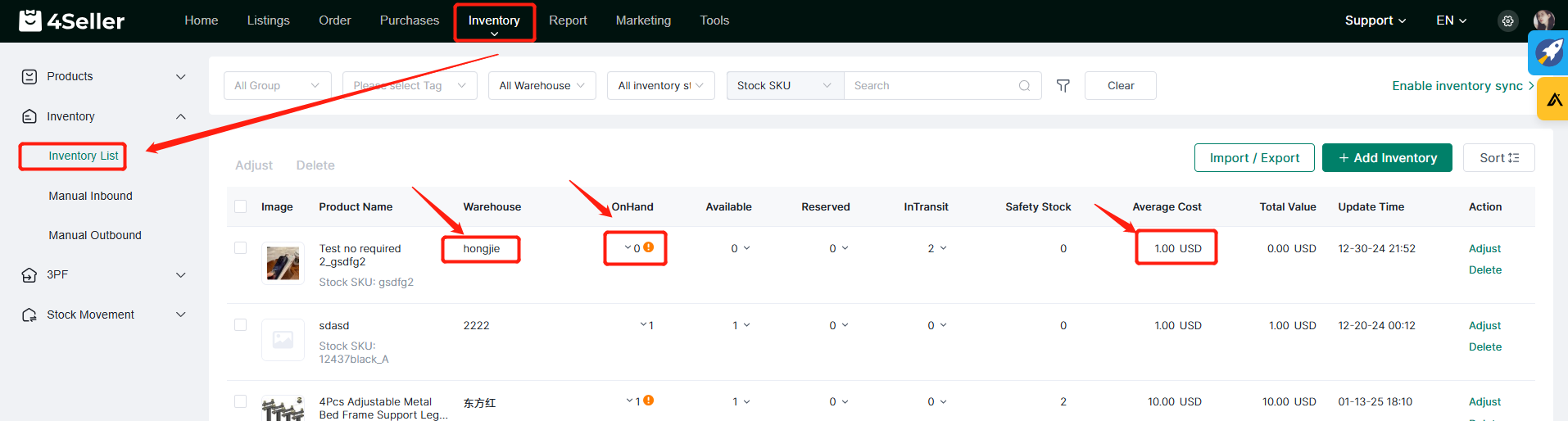
How to Adjust Inventory Information in Bulk?
① Select the multiple SKUs to add inventory> Click "Adjust" to batch edit all SKUs information including "On Hand Quantity and Unit Cost" in the list.
② Click "Save" to finish adjusting Inventory Information in Bulk.
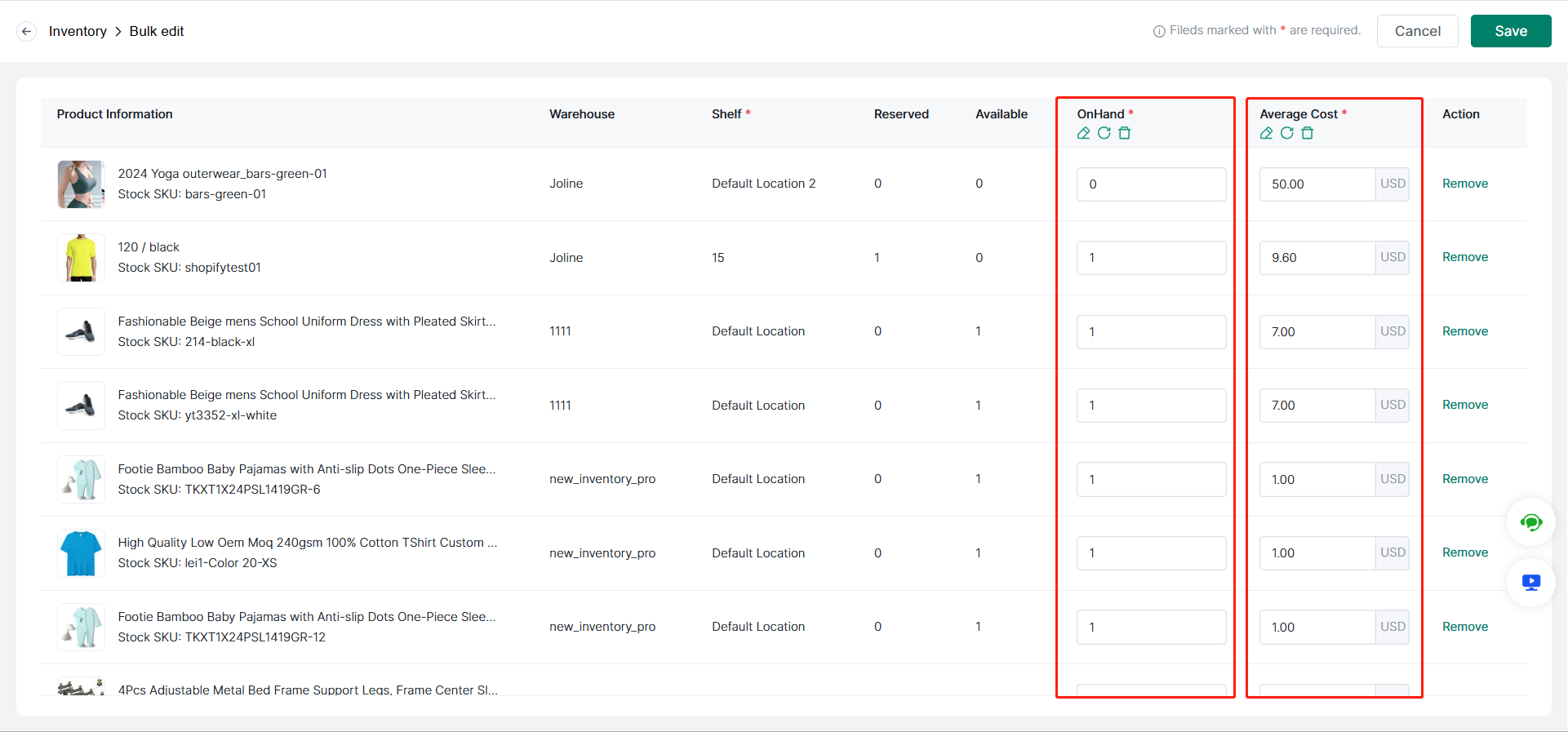
Definition
- OnHand: Represents the total stock quantity. It is typically used to record the actual inventory quantity of your warehouse products. (Reserved Inventory + Available Inventory)
- Available: Inventory that can be allocated. When orders are synced to 4Seller, the system checks if the matched product SKU has enough available inventory for allocation. If not, inventory alert will be triggered.
- Reserved: Inventory quantity that has been allocated to orders. When an order is synced to 4Seller, the system locks the inventory for that order. The locked inventory will not be allocated to other orders.
- Safety Stock: A user-defined safe inventory value. If the inventory quantity falls below this value, 4Seller will generate an inventory alert to remind you to replenish the stock.
If you have any further questions or suggestions, please do not hesitate to contact our support team.